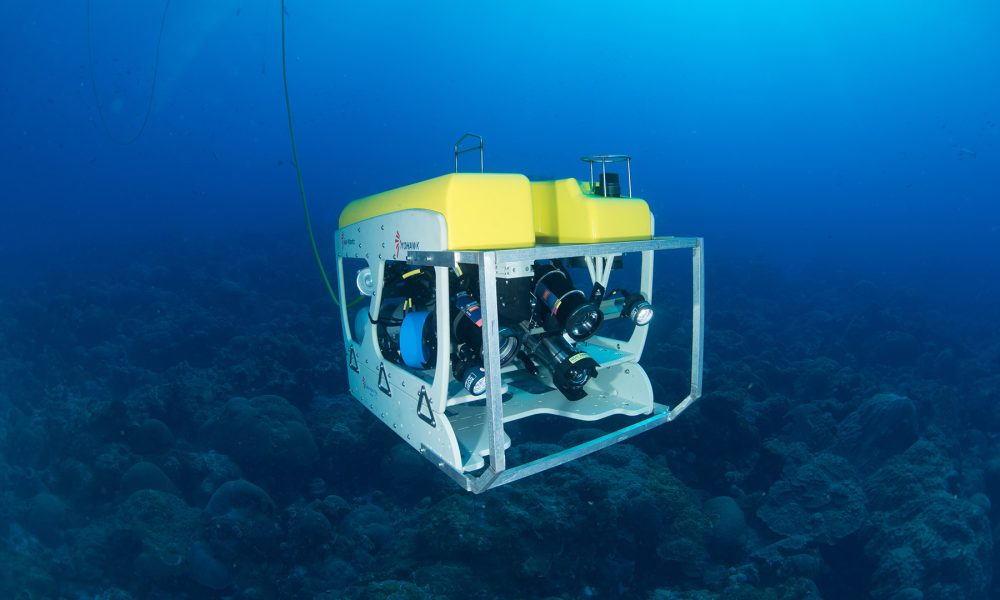
What is Remotely Operated Underwater Vehicle (ROV)?
ROVs, or remotely operated underwater vehicles, are unmanned machines that are controlled from a distance. It is a robot that operates underwater and gathers information about hydrothermal vents and other subsea features. The employment of an automated control system with a remote pilot makes it both reliable and easy to use.
Observation-class ROVs are used to explore the ocean floor and capture high-definition video and still photos for scientific analysis. The unmanned vehicle has water samplers, manipulator arms, and other equipment installed. The average battery life for a modern ROV is 8 hours.
The link between the operator and the remotely operated vehicle is established using an optical cable, allowing the vehicle to move under the control of the operator.
ROVs are extremely complicated machines used for a wide range of activities, from exploration and unmanned expeditions to research and sports. Researchers of all stripes employ them, from zoologists and botanists to engineers and physicists. Many businesses utilise these tools on a regular basis to check on its infrastructure and make any necessary repairs, including those in the aquaculture, agriculture, and other sectors.
In this article, we’ll examine the most important aspects of remotely operated vehicles (ROVs), including their applications, classifications, pre-launch preparations, operations, and limitations.
What is a Remotely Operated Vehicle?
An ROV, or remotely operated vehicle, is a robot that can function in water. It behaves like a toy submarine, but there are no operators on board.
It can operate both wirelessly and via a cable connection, though the latter is more typical. The highly complicated ROV is the sum of several different subsystems.
The various components that form the broad operating mechanism of the ROV are-
1. Electrical systems (wiring and circuitry),
2. Mechanical structures,
3. Sensors and appendages, and
4. Task-specific structures.
ROV’s skeleton is the supporting framework for all these components. It is as light as feasible so as not to provide unnecessary weight or resistance to movement.
An outer Manifold shields the sensitive inner workings from harm. In order to hold wiring and other electronic circuit components, there are holding clips along the frame parts.
The skeleton employs the triangulation principle of stiff mechanics to absorb “severe” impacts. Think of a square box as a starting point for learning about triangulation.
Any stress applied to a frame’s vertices would cause the structure to buckle and eventually collapse. The inclusion of a diagonal element increases the tension strength instead.
The strength of the entire frame is improved with the addition of a single member. An X-joint with two diagonal members is used to strengthen the structure, especially in places prone to strain and compression.
Subsystems and Materials Used in ROV Design
The electrical systems are the brains of the remotely operated vehicle, consisting of its wiring and circuitry. The incredibly resilient and intricate nature of the electronics equipped on them is the only reason they are so useful and may be employed in a wide variety of sectors.
A controller feeds instructions onto the main motherboard and processing unit, which translates those instructions into a tangible output.
Autonomous underwater vehicles (AUVs) are uncommon in this industry because of the many obstacles that must be overcome.
The controller’s input signals may be connected or wireless, depending on the level of creativity and design used. There’s a possibility that this varies from one task to the next. For instance, at a sunken shipyard, a robot’s wires could easily become tangled.
However, as the robot moves deeper into the rubble, it runs the risk of entering an area where it cannot receive a wireless signal. And so, it’s important to take a close look at the office and identify any potential dangers.
When the transmission reaches the ship’s receiver, it is passed on to the mechanical systems. Motors in the form of small, specialised marine propellers are the primary means of propulsion.
The two propellers each have anywhere from three to five blades and are driven by miniature servo motors enclosed in watertight cases. They function as a steering mechanism and can be turned both clockwise and counterclockwise.
The propellers on some of the more sophisticated ROVs used for wreckage analysis and deep sea research may swivel. These are more expensive than their stationary equivalents and see seldom use. This is necessary only under the most stringent of circumstances.
The sensors and tools are the backbone of the ROV. Cameras, depth gauges, temperature sensors, and sensors for monitoring the internal system are among the most often used pieces of hardware.
Having constant visuals of their surrounds is essential, hence the operator uses cameras to do so. When operating in a high-pressure area, depth gauges prevent the ROV from going any deeper than necessary.
Subsea thermal vents and thermoclines can be observed, as well as the resulting temperature zones. Finally, sensors within the ROV itself guarantee that everything is operating as it should be.
The ability to tailor a ROV to a given task expands the scope of its application. For instance, artefacts can be gathered with mechanical arms and equipment during historical research and shipwreck visits.
The ROV can be outfitted with rock cutting instruments for subsea geological research to collect samples for further study. It uses LiDAR, SONAR, or RADAR to ping the seafloor and receive the reflected waves off the peaks and valleys, allowing it to create a 3D map.
There is typically at least one main camera, but other specialised cameras with features like thermal imaging, high-precision photography, macroscopic lenses, and so on may also be present.
An ROV’s material selection is of the utmost importance. The frame must be lightweight so as not to hinder the vehicle’s performance, but sturdy enough to survive moderate to severe impacts.
All electrical components should be sealed in watertight enclosures and coated with insulating materials. To avoid any problems during use, corrosion-resistant materials require extra care.
Since the ROV spends so much time submerged, corrosion is less of a concern (lack of oxygen, which is necessary for rusting).
Nonetheless, corrosion is more likely to occur at the surface (dampness combined with atmospheric oxygen). To do this, it’s necessary to dry the ROV completely and keep it in a clean, dry place where it won’t be exposed to moisture or contaminants, which could lead to mould or rust.
Special paints are applied to the ROV surface to combat marine growth. These paints destroy any existing bacteria and prevent any new ones from sticking to the ROV.
Usage of ROV
Remotely operated vehicles (ROVs) have many applications and can be outfitted for a wide range of tasks. This is why most makers of unmanned vehicles supply a framework that can be customised. The term “frame” or “template” is used to describe the ROV’s fundamental structure. In this section, we’ll examine the wide range of applications for such tools.
A submarine ROV is loaded with state-of-the-art gadgets. It consists of underwater illumination and a video camera to improve the quality of underwater footage for use in teaching geology and marine biology.
With the constant progress of technology, new technological concepts are being taught to remotely piloted vehicles, greatly expanding their capabilities. Other equipment may include a stationary camera, water sampling equipment, or a manipulator.
In addition, sophisticated instrumentation for accurately measuring and evaluating things like current temperature, light penetration, and water clarity can be installed aboard a remotely driven underwater vehicle.
These are frequently installed on ROVs designed for scientific research and exploration of the ocean floor. Chemical analysts also investigate the unique composition of water at varying depths and locations.
Originally designed for use in the industrial sector, remotely operated vehicles (ROVs) are now routinely used to examine pipelines (both on the inside and the outside) and perform structural tests on offshore platforms.
These remotely operated vehicles (ROVs) are also useful for sifting through historical ruins and shipwrecks deep within the ocean. Many aquariums use the ROVs for instructional purposes, and they are used on various scientific trips.
Categorisation of ROVs
By comparing characteristics like size, power, weight, and depth, different types of underwater ROVs can be identified. When fully assembled, the Micro ROV weighs less than 3 kilogrammes because to its compact design.
The primary classifications used are as follows:
1. Micro ROVs
2. Mini ROVs
3. General ROVs
4. Inspection Class
5. Light Work Class
6. Heavy Work Class
7. Trenching and Burial ROVs
Because of these features, the ROV can inspect crevices as narrow as a pipe’s diameter, something a diver could never do.
Miniature and light, the Micro ROV weighs in at around 3 kg. These features allow the ROVs to investigate crevices or pipeline breaches that would be too narrow for a diver to fit through.
However, typical Mini underwater ROVs weigh only about 15kg. From the safety of a boat, one person may control it and conduct an underwater exploration mission.
Remotely piloted vehicles in the micro and mini categories are an alternative “eyeball” because they are not involved in intervention activities.
General ROVs typically have less than 5 HP (propulsion) and include three-finger manipulators similar to the ones found on the vintage RCV 225. These are designed to help with simple surveying jobs and typically feature a sonar unit.
One remotely operated vehicle (ROV) has been modified to travel to depths of 7,000 metres, well beyond the norm of 1,000 metres.
The Lightwork class of unmanned vehicles has an HP rating of less than 50 and can carry several manipulators. You may go as deep as 2000 metres with these ROVs. A polymer called polyethene is utilised in construction instead of the more common aluminium alloys or stainless steel.
The Heavy office machine can reach a depth of 3500 metres with its two manipulators and support less than 220 HP.
Over five thousand kg may be lifted by these remotely operated vehicles. Further, they are adaptable to use with a variety of manipulators. Heavy work is typically used for subsea connections and other deep-water installations.
The Trenching ROV has a horsepower range of 200–500 and can operate at depths of up to 6,000 feet. Some underwater vehicles may operate at powers of over 600 HP or more, while the majority of ROV propulsion systems operate at less than 500 HP.
They are typically employed in the laying of cables, the digging of trenches in the seafloor without risk, and the anchoring (burial) of subsea components utilised in the oil and gas business.
As a last distinction, submersible ROVs can be broken down into categories based on their respective launch mechanisms. Tether Management System (TMS) is a system that regulates the payout of the umbilical connection that provides energy and control to the remotely operated vehicle (ROV). When there is no physical connection between the vehicle and the ship or observation platform, we refer to it as a “free-swimming vehicle.”
It has a neutral buoyancy in these conditions. Others, though, are kept in garages, which are lowered into the water and serve as storage for the ROVs inside.
To launch, the ROV disconnects its rope from the ship and instead releases it from the garage. Launching methods might vary in terms of depth, purpose, and location.
Preparation and Launching of ROVs
R/Vs can range in size from a tiny bread box to a modest truck, which is a wide variety. When preparing to launch an underwater vehicle, it may be simple to just drop the robot into the water from the ship.
It’s possible that large windlasses will be required to haul the robot out of the sea as part of the recovery process. A-frames are typically available to allow a person to safely hang over the ROV onto the deck.
Occasionally, there will be a variety of constructions labelled “garages” that are sunk into the back. The ROVs can use these “garages” like a temporary safe haven, and they can be retrieved after the voyage is finished.
Compared to regular diving expeditions, which can result in serious damage or even death, the infrequent excursions conducted by remotely driven vehicles are seen as more safer.
If a submersible becomes trapped and unable to move freely, a remotely operated underwater equipment can be of great assistance due to its cutter blades or manipulator’s arm.
Bad weather can be a major barrier to submersible expeditions, but it won’t have any effect on a remotely operated vehicle. As an additional application, researchers can first place the remotely operated vehicle (ROV) underwater to investigate the site’s specifics before deciding whether or not to deploy a submersible.
The remotely operated vehicle (ROV) is carefully lowered into the ocean before being ejected from the ship’s side or the platform is launched. Splashing is prohibited to protect the delicate machinery on board. The freeboard must be low enough for this to be lowered by hand, however windlasses can be employed if necessary.
In rough waters, where there is a higher chance of injury upon entry to the splash zone, a moon pool may be used. Typically made up of a hollow vessel with the water’s surface located at the bottom, moon pools are enclosed spaces.
One results in a column of water where the water level is rather constant. In order to avoid resonance-related damage, dampers are utilised to dampen the heaving action. During bad weather, ROVs can be lowered through the moon pool.
Famous ROVs
The Ventana, which uses hydraulic power and can dive to a depth of 1850 metres, is one of the most well-known underwater ROVs. Remotely, the crew of RN Point Lobos operates the Ventana.
In contrast, the MBARI franchise acquired the remotely operated vehicle (ROV) Doc Ricketts in 2008, and it has the extraordinary capability of penetrating deep down to a depth of 4000 metres.
Since then, there have been consistent upgrades to this RC car. As a superior substitute for the previous ROV Tiburon, which could also dive to depths of 2.5 miles, the Doc Ricketts performed admirably.
These innovative submarines have made it simpler to investigate several oil and gas deposits located deep below the ocean’s surface. The divers’ inability to successfully locate many oil sources was a big business setback.
Interestingly, the ROV sector has helped uncover the previously unknown locations of infamous shipwrecks including the RMS Titanic, USS Yorktown, SS Central America, and the German cruiser Bismarck.
The remotely operated underwater vehicle has also been used to retrace the shipwreck of the SS Central America and recover valuable artefacts from its seafloor location.
Shortcomings
The ideal configuration would involve a powerful signal that could be used to command ROVs from a great distance. It will be able to go farther than tethered constructions can at the moment. High power and frequency may be harmful to marine life.
An other option for increasing the ROV’s operating range is to use a low-power primary signal that is amplified by a series of boosters placed at regular intervals.
From an ecological perspective, the cost is acceptable despite the fact that it is higher. Due to the increased number of amplifiers needed for the low power option to work, the ocean surface would become unsightly.
Lack of human presence is a major drawback of remotely operated underwater vehicles, which makes it difficult to carry out visual surveying underwater. Intricate wiring keeps the automobile tethered to the main boat above water, limiting how far it can drive independently.
Wireless ROV control is an active area of study and development at present. The suggested architecture proposes two primary approaches for implementing this control.
The ideal configuration would involve a powerful signal that could be used to command ROVs from a great distance. When compared to tethered designs, its range will be far greater. High power and frequency may be harmful to marine life.
Another option for increasing the ROV’s operating range involves using a weak primary signal that is amplified by a series of boosters placed at regular intervals. From an ecological perspective, the cost is acceptable despite the fact that it is higher.
Due to the increased number of amplifiers needed for the low power option to work, the ocean surface would become unsightly.